Transforming Waste into Sustainability: Hercal Revolutionises the Construction Sector with its Innovative Approach to Valorisation
Hercal is leading the transformation in the construction sector in Spain, standing out for its commitment to waste reduction and the production of sustainable materials, thus contributing to a more sustainable future.
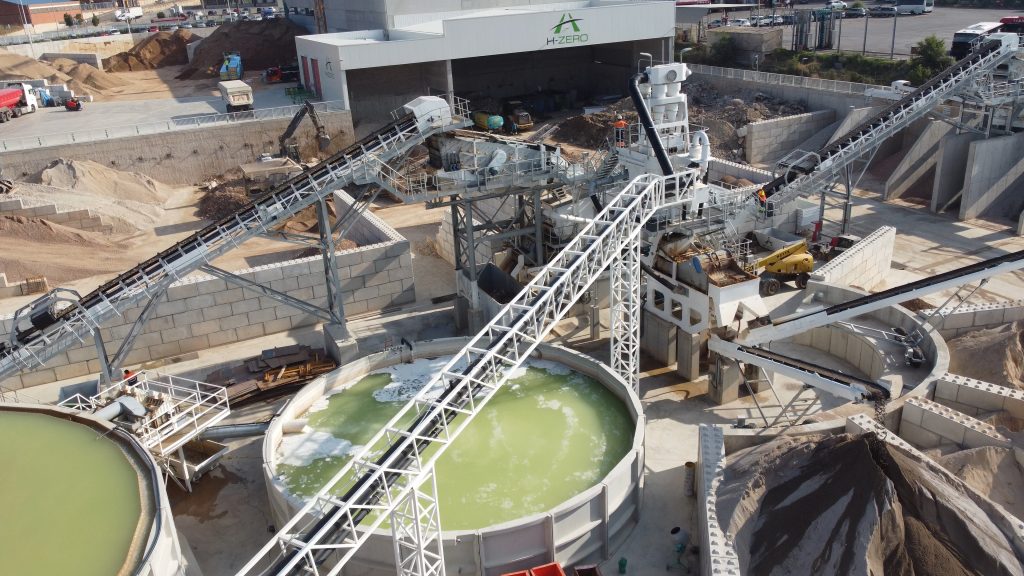
Hercal Diggers is a family business with 16 years of experience specialising in demolition, demolition and the execution of civil works projects, ranging from excavation and earthmoving to the final delivery of the work. Dedicated to implementing a sustainable management model by adopting the ISO 14001:2015 standard, a set of environmental management documents that regulates the aspects of Hercal’s administration from the perspective of environmental responsibility.
This comprehensive system is based on a process of continuous improvement, committed to environmental responsibility in order to reduce the impact of its operations on the environment as much as possible. It also has a plant called “H-Zero”, the first in Spain dedicated to the recovery and washing of construction, excavation and demolition waste, with the aim of obtaining a recycled aggregate of excellent quality.
For Hercal, demolition is not the end, but the beginning of a new life cycle for materials. Beyond waste management, they transform each demolition into a resource bank, reusing waste for the manufacture of sustainable concrete. This approach not only minimises environmental impact, but also reduces the exploitation of natural resources, demonstrating that the circular economy and real sustainability are essential advances in the construction sector.
For this interview we had the opportunity to talk to Miguel Pérez Peñalva, manager of Hercal Diggers, who took part in the webinar “European experience in the recovery of waste from the construction sector” held as part of the AL-INVEST Verde Construction project on 8 November, and who spoke about the various circular systems that the company is implementing in relation to the recovery of waste generated by the construction sector, as well as the production of sustainable concrete through its innovative “H-Zero” plant.
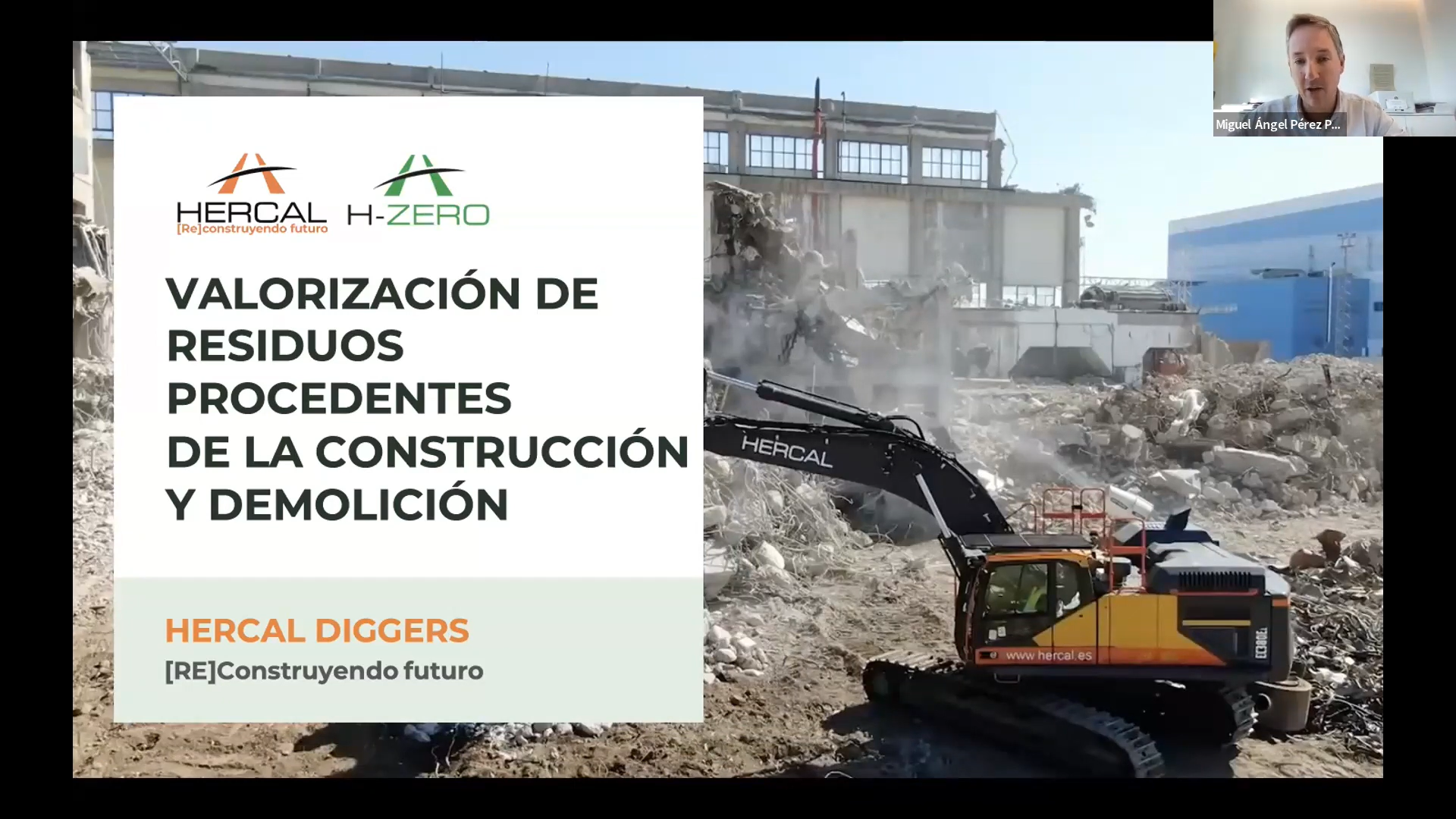
Miguel Pérez Peñalva, manager of Hercal Diggers, in the webinar “European experience in the recovery of waste from the construction sector”.
- How did the need to implement circular systems in your company arise?
There are personal reasons that make us extremely sensitive to environmental care. As we watch landfills fill up with reusable materials, we realise that, as a society, we are not doing something right.
In addition, there are business reasons behind our environmental concerns. We like to analyse international practices, to examine technologies applied abroad. It was then that we identified technologies for the recovery of construction and demolition waste (CDW) that we could implement in Spain. Although in the short term this represents an investment and an additional burden, we are convinced that in the future it will become a competitive advantage.
- How do they go about identifying which demolitions to carry out? What pre-demolition steps do they need to take?
We analyse demolition requests from both private and public clients. We evaluate those that best align with our values, giving priority to clients who appreciate respect for the environment and require technical and complex demolition, among other criteria.
Before starting any demolition, we carry out a detailed analysis of the project and the state of the installation to be demolished. Based on this assessment, we identify all the materials that can be recovered, such as glass, wood, false ceilings, cables, furniture and doors, before proceeding to mechanical demolition with heavy machinery.
Selective demolition marks the beginning of the process, where we carefully separate reusable materials (first phase). Subsequently, we start the mechanical demolition using the appropriate machinery according to the specific characteristics of each demolition.
- How can companies be encouraged to become more sustainable and environmentally conscious? And what strategies should be used to help them identify long-term benefits and opportunities?
For companies to become more sustainable, it is essential that they first become more sustainable financially. Companies cannot be required to adopt sustainable practices at the expense of worsening their financial performance. At Hercal Diggers, we have taken an exceptional step, as the owners have decided to risk everything in order to leave a better world for future generations, but this is not and cannot be the norm.
On the other hand, the public administration has the capacity to effectively incentivise business sustainability. It can easily achieve this by awarding favourable scores in public tenders to companies that use recycled aggregates on their construction sites, use low-emission concrete, commit not to send rubble to landfills or use hybrid machinery.
In addition, there are other tools such as tax incentives, green public procurement criteria and the requirement for public projects to use sustainable materials. This would generate an increase in demand for sustainable products, giving many companies the opportunity to negotiate and invest in sustainability.
- What has been the experience with eliminating the use of landfills for construction debris?
Unfortunately, Spain has not yet banned the disposal of construction debris in landfills, and in the short term, it does not seem that this ban will be implemented. In Northern Europe, on the other hand, the situation is different. Substantial fees are charged for depositing construction debris in landfills, amounting to €60-70 per tonne in some countries. These fees have a deterrent effect, providing an incentive for the rubble to go to Recovery Plants.
In Spain, the situation varies (with a fee of €3/tonne in Catalonia and €1.5/tonne in the rest of the country). This means that it is often cheaper to transport construction debris to landfill, despite paying a higher fee, than to take it to a recovery plant located a few kilometres further away from the site than the landfill.
In my view, only construction debris that cannot be recycled, i.e. that is too contaminated and cannot be recovered, should be sent to landfill.
- What are the environmental benefits of scrubbing treatment compared to traditional construction waste management methods?
Washing construction debris results in high quality recycled aggregates, which can “replace” natural aggregates in various applications such as structural and non-structural concretes, precast, granular layers and mortars.
This process has a significant environmental benefit, as for every tonne of washed recycled aggregate produced, one tonne of rubble is prevented from ending up in landfill, while one tonne of natural quarried aggregate is prevented from being extracted.
- How is the quality of the resulting material guaranteed after the washing process?
Through the washing process, we remove “impurities” such as wood, plastics, porex and some mortar. This procedure is carried out in a large washing chamber equipped with two augers, which allow the stones to collide with each other, freeing them from all impurities. As the washing chamber is filled with water, these impurities float on top and can be easily removed.
The main “advantage” of washing is the increased homogeneity of the final product, which is crucial for the use of washed recycled aggregates in more demanding applications. The washed aggregates we produce are CE Certified, which guarantees that the process has been carried out diligently.
- How has the implementation of sustainable concrete been received both by today’s society and by construction professionals?
The beginnings have not been easy. Firstly, recycled aggregate does not have a good reputation (there have been many irregularities in recent years, and people tend to call anything recycled aggregate). This perception generates mistrust among users.
Moreover, at present, we cannot compete in terms of price with conventional concrete. In Spain, our competitors are the quarries, which obtain the product by blasting and crushing the material. In contrast, we have made a considerable investment in land (industrial use), machinery and personnel necessary to carry out not only the crushing, but also the process of cleaning, washing and management of impurities.
Fortunately, more and more clients are becoming more aware of and sensitive to sustainability issues, and even value and demand that the works are sustainable and environmentally friendly. This is where sustainable concrete with washed recycled aggregate has great potential.
- How are Spanish regulations on the use of sustainable concrete developed?
Spanish regulations on concrete with recycled aggregate lag significantly behind other European regulations. For example, the Structural Code of 2021 does not present any new developments in this aspect compared to EHE-08, the previous regulation dating back 13 years.
The current standard does not allow the use of mixed recycled aggregate (which includes ceramic material) or the use of recycled sands, even if they come from the recovery of concrete.
Fortunately, in 2024, Eurocode 2 will come into force, a European-wide concrete standard that includes Annex N, addressing the use of recycled aggregates in concrete with much more ambitious percentages than those allowed by current Spanish regulations. However, it is important to note that this annex will not be mandatory, as each country will have the option to adhere to it or to apply its own restrictions.
- How to reduce carbon emissions in sustainable concrete production?
90% of the carbon emissions generated by concrete are due to cement. For this reason, efforts are currently focused on manufacturing low-emission cements. To do this, it is essential to reduce the percentage of clinker needed to manufacture cement, which is achieved by using secondary materials, such as recycled aggregates.
- What is the contribution of technological innovation to the development of more sustainable building practices?
Technological innovation is key to developing more sustainable building practices. It is the first step that every company must take before implementing a new product or application.
In our case, prior to the investment in the H-ZERO Valorisation Plant and the acquisition of the washing machinery, we carried out an R&D project in collaboration with the Polytechnic University of Catalonia. From the rubble generated in our works, we managed to obtain washed recycled aggregates through manual processes, which were subjected to trials and tests, which was of great value to the collaboration between the university and the company.
If you want to see the presentation of Miguel Pérez Peñalva, manager of Hercal Diggers, we invite you to watch the following video: